The Fundamentals
Comprehending the fundamentals of crankshaft manufacturing and machining can be extremely helpful in not only maximizing performance, but in improving crank and engine life.
The supply of suitable junkyard crankshaft cores, once a mainstay of racers everywhere, has pretty much dried up, but performance enthusiasts now have lots of sources for brand-new, reasonably priced cranks for Chevrolets as well as popular Ford and Chrysler engines.
One of the very first things beginning engine builders typically ask is: what is the very best crank to utilize, forged or cast? A cast crank is just that; an iron casting in which the metallurgical structure is made up of a random pattern of particles, filled with tiny holes and spaces. A forged steel crank is produced by compressing a much purer metal into the die under severe heat and pressure to produce an extremely dense molecular structure, and a much stronger crank.
This forged crankshaft from Eagle is created for small block Chevy applications. It’s reasonably easy to spot the difference between a cast crank and a forged one. Cast systems have a distinct parting line located on each of the counterweights and throws while forged units can be identified by a wide, raised die mark on the throws. The only weak points of a conventional basic forging is that during the manufacturing process, the connecting rod throws are offset by twisting the crankshaft. Twisting not just misshapes and stresses the forging, but likewise restricts the kinds of metal that can be used.
Shop Operations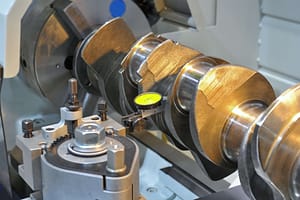
As soon as the kind of crank has actually been figured out, there are a number of machine shop operations that can be carried out to make it more durable, and to validate that the crank picked is suitable, particularly for racing use.
Magnafluxing
Magnafluxing is a crucial step in the crankshaft manufacturing and selection process. It is a dry, non-destructive test in which the part goes through a strong electromagnetic field while magnetic particles are sprayed on the surface area. Any cracks act as magnetic poles, causing the particles to line up along that point. Any cracks aside from small stress cracks surrounding the oil holes are grounds for rejection.
Magnaglow
Magnaglow is a wet, non-destructive test throughout which the part is covered with a liquid containing magnetic particles. The part is then subjected to a strong magnetic field which triggers the particles to line up along any cracks that may exist. An ultraviolet light is used to find the particles and the cracks.
More Methods
In crankshaft machining, turning, or grinding, includes machining the journals undersize to fix scored or damaged bearing surfaces. Use of an undersized system is of no issue and as long as the crank has actually been turned properly, it will keep the proper oil clearances. Some racers will intentionally “turn” a crank as much as.030″ or.040″ undersize in pursuit of a smaller bearing size that allows them to squeeze out a few more “horses”.
A typical practice includes machining the rod journals of a small block Chevy crankshaft to 1.888″ so that smaller Honda-sized rod bearings may be used to maximize performance.
Indexing makes sure that the rod throws are precisely 90 ° apart. Stroke monitoring is performed to see that each rod throw has the same stroke and can likewise be remedied during the indexing process.
Offset Grinding
Offset Grinding is a typical practice used by NHRA Stock and Super Stock racers to increase performance while staying within the NHRA’s +.015″ maximum permitted stroke tolerances. The journals are merely turned offset, generally.013″, to add a couple more cubic inches, yet while still fulfilling the sanctioning bodies’ strict rules.
Micropolishing
Micropolishing produces a mirror-like surface on the bearing journal surface and it can likewise correct a crank- shaft that has extremely small nicks or flaws.
Straightening includes positioning the crank in a special fixture, pre-loading it with a hydraulic jack, and carefully striking it with a heavy hammer.
Cross Drilling involves drilling two converging holes at right angles through the main bearing journals so the rod journals get “full-time” oiling, especially valuable when utilized with standard half-grooved main bearings. A lot of OEM crankshafts have a single oil feed hole from the main to rod journals, enough for the daily driver, but not for a high-revving race engine.
Chamfering can be performed in the home garage with a small hand-held grinder. Oil passages drilled at the factory are typically pestered with sharp edges left by tooling. By gently deburring and radiusing these holes with a little grinding stone, a little depression is produced to act as a reservoir to help disperse oil throughout the surface of the journal.
Deburring removes sharp edges, or “stress risers”, which can transform into a fracture or crack. Utilize an abrasive wheel to quickly smooth over parting lines and die marks.
Shot peening, similar to sandblasting, bombards the crankshaft with really small ball bearings. The surface of the metal is compressed throughout the procedure, helping to prevent fractures from developing.
Stress Relieving “relaxes” the steel and includes warming the crankshaft to a particular temperature to permit the particles to reorganize themselves. It then becomes “relaxed”, similar to the “seasoning” process that an engine block goes through as it collects miles.
Hard Chroming is a repair technique that also improves resilience. A layer of chrome is built up to restore a damaged journal.
Nitriding or Tufftriding enhances the surface hardness of the bearing journals. The crank is heated up to 800°F and then immersed in a bath of cyanide salt. This process ideally penetrates the journals about.020″, however the results are occasionally inconsistent.
Forged and Cast Crankshafts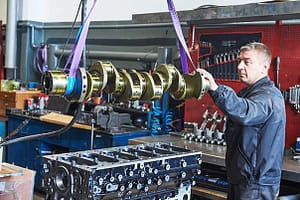
It’s reasonably simple to find the difference between a cast crank and a forged one. Use of an undersized unit is of no issue and as long as the crank has actually been turned properly, it will retain the proper oil clearances. Some racers will deliberately “turn” a crank as much as .030 ″ or.040 ″ undersize in pursuit of a smaller bearing size that enables them to squeeze out a few more “horses”.
I hope you enjoyed this article about crankshaft manufacturing. I found a great deal of inspiration for this post on Motorstate’s website. I have a related article on the Basics of Crankshaft Manufacturing.